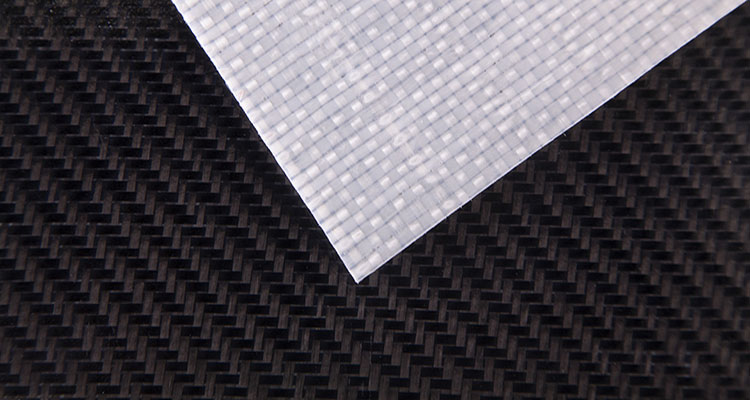
Spotlight on Organosheets
Organosheets are continuous fiber reinforced thermoplastic sheets containing primarily carbon or glass fiber fabrics. Recently, organosheets have begun to encompass a broader range of semi-finished products that share key advantages deriving from thermoplastic matrices – from polypropylene and polyamide 6 to polyethylenimine – and the diverse architecture of the reinforcing fibers.
Veterans of the composites industry often refer to organosheets as thermoplastic prepregs since it is an intuitive way to describe them by analogy with continuous FRP thermoset composites encountered in structural applications. Organosheets have a strong built‑in advantage: They contain fully polymerized thermoplastic polymers (organic materials). Unlike prepregs, which have limited shelf life and require refrigeration and specific inventory control, organosheets can be stored for extended time under typical temperature and relative humidity conditions determined by the thermoplastic polymer they contain. The sheets can be cut to shape, stacked and integrated in automated manufacturing processes that resemble the processing of metal sheets. This similarity to metal sheets – often referred to as blanks by metal component stampers – is particularly helpful when discussing applications with automotive industry stakeholders.
Industries such as sporting goods and consumer products adopted organosheets early on because they manufacture in high volumes and require short cycle times. These requirements also pervade the automotive industry, where organosheet applications of increased complexity are now being found. Leading equipment manufacturers have proven the technical readiness of organosheet technology and are delivering processing cells that can produce more than 200,000 parts per year from one manufacturing line.
Organosheets can be thermoformed, compression molded or incorporated in hybrid molding processes. If you are new to organosheets but such processes are in your portfolio, experimenting with these versatile composites might be easier than you think. Here are a handful of tips to get started:
Start with what you have – Use existing equipment and tools, and reach out to material manufacturers for guidance on processing steps and conditions, including mold preparation if you are targeting specific surface quality. Organosheets have to be heated above the polymer’s melting point before being formed. If you do not already have a heat source for a thermoforming operation, consider adding a low-cost infrared heater to preheat the sheets before placing them into the mold. Always plan for proper ventilation when experimenting with new thermoplastic composites.
Select organosheets that fit the application – All organosheets are not equal, and selecting the appropriate configuration is important for processability, performance and, ultimately, cost. Organosheets are defined by the thermoplastic polymer, type of fiber reinforcement, fiber architecture (unidirectional, woven fabric, non-crimp fabric, etc.) and sheet thickness. A single sheet may contain one layer or multiple layers.
Service temperature and environmental conditions required for an application will determine the polymer selection. Part complexity, the need for drapeability and the load requirements will guide the selection of reinforcement and fiber architecture. Organosheets based on woven fabrics allow good drapeability. Organosheets based on non-crimp fabrics (NCF) will allow more flexibility in design according to the load path and might save weight, but will add cost.
Pay attention to load requirements – Understanding load requirements is important for controlling material cost and mass. If a critical load path can be addressed using 2 mm thick organosheet based on a complex NCF fabric, or by a thicker organosheet based on woven fabric, the more expensive NCF organosheet might lead to a more cost-effective and mass-saving solution overall. Organosheets with localized unidirectional tape reinforcement are elegant solutions as well and can help balance the cost/mass equation.
Use simulations and check all assumptions – Use simulations as early as possible to optimize a design. Today, software providers can guide you through functionalities designed specifically for organosheets, making the screening very approachable. To get accurate results, it is important to understand and to leverage the orthotropy of these materials (unique behavior in x, y and z directions). For example, while an organosheet based on 2/2 twill or plain weave fabric shows similar performance in two directions (warp and weft), the assumption of isotropy will be incorrect.
Jiuheng Chen, design engineer at Forward Engineering GmbH, illustrates this very simply. If the organosheet would be isotropic, the shear modulus could be calculated using the elastic modulus and Poison’s ratio as E/2(1+n) = 24,000/2(1+0.15) = 10,435 MPa. In reality, the material is orthotropic, exhibits a shear modulus of ~3,200 MPa and should be modeled accordingly.
Reach out to your network – Use the collaborative environment in the composites industry value chain. Providing composite solutions requires a solid understanding of materials, processes, design and manufacturing cost. A good network of partners can help obtain answers to questions early on and focus on solutions most likely to succeed.
While the cornerstone characteristics of organosheets – light weight, recyclability, fast processability and suitability for high-volume applications – are highlighted more often, at the core of their accelerated adoption are key properties that enable high-volume industries to offer new products faster, to personalize models and to incorporate multiple design features.
Organosheets enable a great deal of functional integration, from brackets and metal insets to sensors and electromagnetic interference shielding solutions. Thermoplastic solutions centered on organosheets are easy to prototype and result in significant reduction of parts, lower tooling costs and scalability to high volume. The core advantages of organosheets will bring the most value to an application.
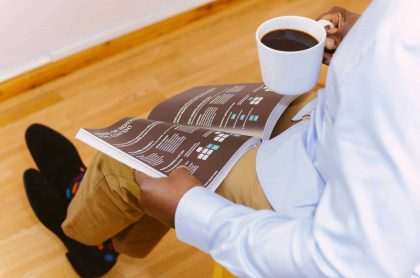
SUBSCRIBE TO CM MAGAZINE
Composites Manufacturing Magazine is the official publication of the American Composites Manufacturers Association. Subscribe to get a free annual subscription to Composites Manufacturing Magazine and receive composites industry insights you can’t get anywhere else.