
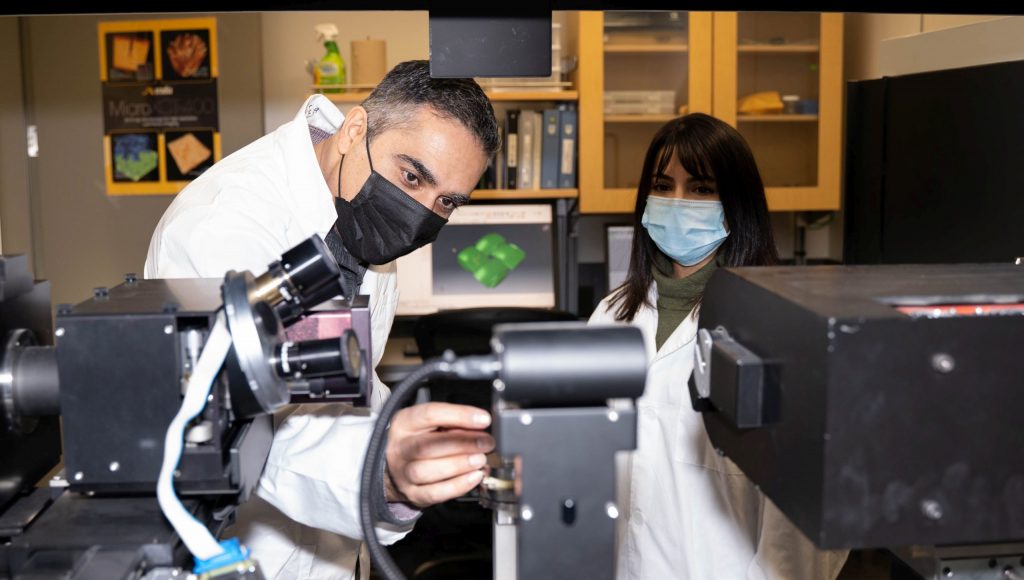
AI Applications Move Mainstream
Larger companies usually lead new technology adoption because they have the necessary hardware and software budgets. But the advent of cloud computing is a game-changer for small to medium-sized organizations.
A recent article from Deloitte noted that the increase of cloud-based and software-as-a-service models for AI and machine learning (ML) have made the technologies more affordable for midsize and small companies, which are taking advantage of the opportunity to digitally transform their businesses.
A variety of AI solutions are becoming available to composites manufacturers. Here are just a few.
Speeding Tool Production
Designing and manufacturing tooling is often a costly, time-consuming process and a big barrier when it comes to OEMs choosing composites over steel and metal for components, says Martin Oughton, CEO and co-founder of Plyable. His company has developed a cloud-based, AI software that speeds this process.
A customer uploads a CAD file of its desired composite component into Plyable’s online software tool and indicates its preference for material, tolerances, manufacturing method, finish and delivery date. The system’s ML algorithms automate the tool design process, assessing different tool geometries before choosing the best option. The AI software then draws upon an extensive database of supplier information to develop a quote based on the tool’s size and geometry and on up-to-the-minute material prices and market conditions. The entire process, from design to quote, takes less than a minute.
Once the client accepts the quote – usually three to five days – Plyable sends the bid out to its network of carefully screened tooling providers, which includes more than 1,500 five-axis CNC machines and some additive manufacturing options as well. The jobs are awarded quickly, on a first-come, first-serve basis, and production begins almost immediately. The client can use Plyable’s system to track the tool’s progress and review production and inspection reports.
Oughton says that smaller Tier 2 and Tier 3 aerospace suppliers, as well as OEMs and Tier 1 companies have already used the AI tooling system. He believes that technologies like these will improve composites’ competitive position.
“Composites have long been talked about as the material of the future, but I think they are in danger of always being just the material of the future, not the material of now,” says Oughton. He asserts Plyable’s technology is open to all companies and can lower the barriers to a wider adoption of composite solutions.
Automating Inspection Processes
Automated fiber placement (AFP) has significantly improved the production rates and quality of composites manufacturing. “But due to the lack of reliable, in-process inspection technologies, AFP processes are currently interrupted intermittently for manual inspections – anywhere from 20% to 70% of production time,” says Waruna Seneviratne, director of the Advanced Technologies Lab for Aerospace Systems (ATLAS), National Institute for Aviation Research (NIAR).
His research team hopes to significantly reduce that downtime with an in-process AFP manufacturing inspection system (IAMIS) made with off-the-shelf laser and camera systems. Attached to the AFP placement head, the IAMIS creates a digital manufacturing twin (DMT) of the part. Using machine-learning algorithms, the system analyzes this digital data. It detects manufacturing effects that are above acceptable limits, reducing time-consuming and operator-dependent manual inspection processes that require interrupting the manufacturing process. Furthermore, it records the locations of the part’s allowable defects (those that do not require repair). Having this record can be useful when the part gets damaged during service, since it provides technicians with a better way to assess the potential damage in a given area.
The system’s AI also analyzes the digital twin to detect any gaps, overlaps and other manufacturing anomalies in the part. Based on this information, system operators could adjust manufacturing processes like laydown speed, heat input and compaction force to reduce manufacturing defects on future runs. This could improve the quality of parts by 10 to 20%, says Seneviratne.
After several successful demonstrations of the IAMIS, researchers will mount the system on production lines of several aircraft manufacturers, including those in the advanced air mobility market, within the next few months. The manufacturers will continue manual inspections at the same time to compare results with those from IAMIS.
“Advanced air mobility companies want to make thousands of airplanes a year but using the AFP machine the way we do today they’re not going to make 1,000,” says Seneviratne. Eliminating the manual inspection process and employing IAMIS – with a fully-trained ML algorithm – could decrease the time required to fabricate a part by 20% or more and reduce the cost by over 30%.
“Eventually, we want to convince the FAA and the certification authorities that the IAMIS system is either equivalent or better than manual inspection,” Seneviratne adds.
Improving the Supply Chain
Many large industrial manufacturers have implemented AI and ML-based supply chain management programs to optimize supplier selection and flag potential problems. To be effective, these systems use data that’s pulled from the organization’s enterprise resource planning (ERP) systems, supplier lists and other sources stored in the cloud.
But getting that data input can be problematic for the many composites manufacturers that have not digitalized their operations. “A lot of their data is still in Excel sheets, in registers, in notebooks somewhere,” says Rajeev Sharma, chief technology officer at Grid Dynamics.
A company that wants to digitize and gather data to move to an AI model for supply chain must remember that AI should be used to solve their particular business problems, Sharma says. For example, if a manufacturer decides to work with a tech provider like Grid Dynamics to construct an AI supply chain model, it will most likely start by building a database with basic supplier information like location and materials costs. Then, if the company’s primary business concerns include material availability and pricing, it might include inflation data, weather data or even political data in its AI model. That enables the model to train on those factors and include them in the algorithms for making purchasing recommendations.
“Suppose you have 1,500 suppliers in your database; you know where they are located and you know their regular prices,” says Sharma. “Now imagine that some of those suppliers are in a part of the world where there is a hurricane. If your system is integrated with weather data and price data, and if you have an AI model trained for weather impact on your business, your AI engine can tell you which of your suppliers are at risk and how it could impact your raw material prices and your delivery schedule.”
The AI model could even provide a visualization on a Google map of which routes would and would not be disrupted. “All of this is done autonomously, without anybody having to press any button,” says Sharma.
Creating a Safer Workplace
Companies that have invested in closed circuit television systems for security could use AI to increase their return on investment.
“CCTVs aren’t well utilized. They have to be manually monitored by a person or looked at retroactively after some occurrence to understand what happened,” says Josh Fox, director of product marketing, AI technologies at SparkCognition.
It has developed a platform that taps into a company’s existing CCTV infrastructure and uses SparkCognition’s Visual AI Advisor to monitor, analyze and interpret the activity the camera captures. A composites manufacturer or materials supplier could use the cloud-based system to look for security lapses or safety violations.
The system includes pre-built use cases that cover areas such as health and safety, physical security, productivity and situational awareness. “A use case is a combination of a computer vision model and business logic rules that enable some sort of response or action to occur,” Fox explains.
The AI monitors the camera feed in real time and compares workers’ actions to the acceptable behaviors defined in the use cases. For example, the system’s ML component can be trained to distinguish between someone who is wearing a hard hat and someone who is not. If the AI detects someone without the required personal protection equipment, it can send an immediate alert or flag the occurrence for future employee training.
Improving Traceability and Operations
Plataine’s AI, cloud-based, digital thread technology expands composites manufacturers’ insights into their supply chains. Through a digital twin, it creates a genealogy of every product, tracing its route from material supplier through manufacturing and inspection processes to customer delivery. It collects data from a variety of sources, including suppliers’ and manufacturers’ software, digitized paper records and internet-of-things (IoT) sensors that measure equipment conditions on the factory floor. Armed with this information, manufacturers can quickly alert affected customers if they discover defects in some material or production process.
In addition, with data on supplier pricing, location and availability of current materials all contained in the database, Plataine’s digital AI assistant can recommend the best sources for a particular component based on general or specific requirements, such as the need for a supplier that uses renewable energy. It can send alerts if a material is nearing its expiration or suggest alternative sources if some event, such as a strike, is likely to cause material delivery problems or production delays in certain areas.
This technology is available to manufacturers of every size. “You don’t have to install servers or have very robust IT operations. Everything is managed on the cloud, so there’s zero installation and zero disruption to the manufacturing process,” says Amir Ben-Assa, vice president of marketing and product strategy at Plataine.
Capitalizing on AI
The combination of cloud technology and AI offer composites manufacturers an unprecedented opportunity to reduce their costs and increase their competitive advantage.
“The more midsize manufacturers try to digitize and automate – especially in North America where labor is expensive – the more they will benefit from automation and the value that AI brings,” says Ben-Assa. “The less they rely on human power, the more profitable they are likely to be.”
The Future of Materials Selection
Understanding the underlying structure and geometry of composite fabrics is key to determining their properties and performance. Today, manufacturers must rely on extensive experimentation and testing of textile samples or high-level simulations of their properties that may not accurately reflect real world outcomes.
Abbas Milani, professor of mechanical engineering at the University of British Columbia, and his research team are hoping to streamline these analyses through AI/machine learning.
The researchers took micro-CT scans of different woven fabrics at different angles and configurations. The images captured internal complexities, such as waviness, voids and fiber misalignment. Next came mechanical testing on 50 of those sample fabrics to determine the specific properties of each. This image and testing information was entered into a database.
The team then took micro images of other textile samples and, using AI/machine learning, successfully predicted their properties and performance by comparing them to the database images. The entire process of identifying the fabric properties, including imaging, took less than five minutes.
With this process, composites designers who want to use a particular material will someday be able to feed its images into the database to determine its likely properties.
“The inverse application would be for materials discovery,” says Milani. “If you want a particular property from a material that doesn’t exist, you could use the images to determine what its texture should be, what the fiber orientation should be.”
Milani, who serves as technical chair of Canada’s Composites Research Network, says several industry partners have expressed interest in the process.
Mary Lou Jay is a freelance writer based in Timonium, Md. Email comments to mljay@comcast.net.
Professor Abba Milani and doctoral student Tina Olfabakhsh at the University of British Columbia are predicting material properties by using AI to compare images taken from micro-CT scans of 50 sample materials to scans of other materials.
Photo Credit: University of British Columbia, Okanagan
Researchers at NIAR have developed an in-process AFP manufacturing inspection system that could reduce the time required to make composite parts and improve their quality.
Photo Credit: Waruna Seneviratne, NIAR
Plyable’s system uses AI to design a tool based on customers’ requirements.
Photo Credit: Plyable
Plataine’s AI-based system provides more visibility into all aspects of the supply chain and sends an alert when it detects a potential problem.
Photo Credit: Plataine
SUBSCRIBE TO CM MAGAZINE
Composites Manufacturing Magazine is the official publication of the American Composites Manufacturers Association. Subscribe to get a free annual subscription to Composites Manufacturing Magazine and receive composites industry insights you can’t get anywhere else.