
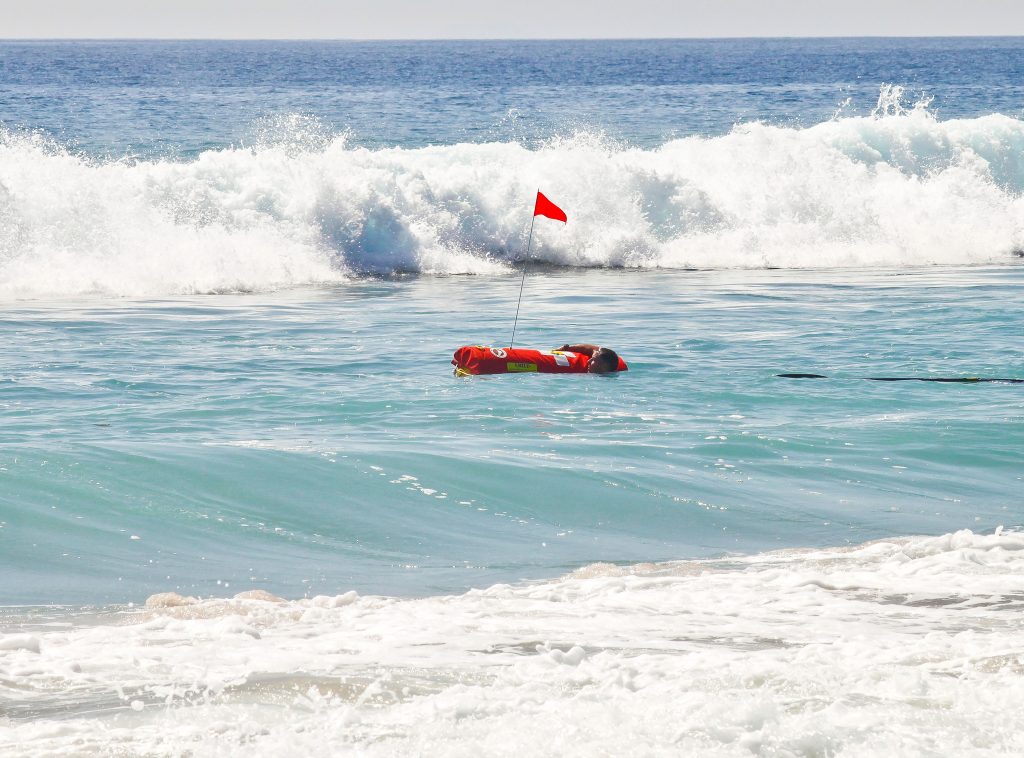
Aquatic Drone Saving Lives Worldwide
When a family of four was recently caught in a current off Rockaway Beach, Ore., an aquatic drone made from advanced composite materials saved the day. Without access to rescue swimmers, jet skis or helicopters, the local fire department deployed the Emergency Integrated Lifesaving Lanyard (EMILY) developed by Hydronalix. “They rescued an uncle, aunt and two kids within minutes and prevented them drowning,” says Anthony Mulligan, founder and CEO of Hydronalix. EMILY can be launched from beach, boat, bridge or helicopter and guided via radio control through surf and debris to reach potential drowning victims within seconds. Victims then hold onto the aquatic drone’s perimeter lifeline until help arrives or they are pulled to safety by an attached rope. Each EMILY drone can support up to 10 people at once or tow a raft to rescue larger groups as it has done during Indonesian ferry accidents. More than 400 of Hydronalix’s aquatic drones are in use in 22 countries and deployed on a rescue mission an average of 1½ times a day, says Mulligan. The story of EMILY begins with Mulligan’s 20 years as founder and CEO of Advanced Ceramics Research, which specialized in ceramic composites for a variety of applications, including unmanned air vehicles (UAVs) used by the U.S. armed services during the Gulf War. After selling the company in 2009, Mulligan founded Hydronalix to build aquatic drones with the same advanced materials as UAVs. The company built its first drone for the National Oceanic and Hemispheric Organization in 2010. Shortly thereafter, Mulligan and his business partner, Robert Lautrup, launched a drone off Malibu Beach, Calif., during the remnants of a hurricane just to see how it would hold up. “No matter how bad the wave was, the drone would always go through it,” Mulligan recalls. “We got the idea that if we put a float on it, it could go out and rescue anyone that was in trouble.” At 50 inches long, 15 inches wide and 15 inches high, EMILY is “a showcase of advanced composite materials,” says Mulligan. The aquatic drone, built much like a small boat, features an epoxy resin reinforced with fiberglass, carbon fiber, Kevlar® fibers and ceramic fibers. The hull is fabricated in two pieces using aluminum molds and wet lay-up of various woven fabrics and fiber orientations determined through computer modeling. To allow the drone to survive impact with rocks, reefs, debris and extreme waves, the outer edges of the hull are reinforced with 2,000 Kevlar fiber tows coated for maritime use and the keel contains three layers of Kevlar. Once cured, the upper and lower parts are laminated together within minutes to maximize strength. For special applications, such as deployment from a high-altitude aircraft, the hull can be constructed in a single piece using water soluble molds. EMILY can travel up to 38 mph. Its motor is connected to a multi-angle CFRP shaft with circumferential edges designed for tensile strength and leading edges reinforced with nanoplatelet reinforced nylon for maximum resistance to damage by debris. Mulligan says a CFRP shaft is key because it returns to its original shape after flexing on impact – for example, when EMILY is dropped off a helicopter or bridge or deployed in rough waters – making it highly durable. Nanoplatelets are also aligned along the pump wall and exit nozzle walls for maximum abrasion resistance to slurry, and the propulsion system uses sealed alumina/zirconia ceramic composite bearings. Mulligan asserts this ceramic composite is so hard that if sand or rocks enter the bearings – an event that would quickly destroy metal bearings – the ceramic composite bearings can use them for lubricant. GFRP screws and bolts are also used throughout the boat to reduce corrosion. Once constructed, each aquatic drone is painted with the same yellow epoxy paint used for sea planes, then covered with a red marine-grade cloth flotation bag. EMILY’s combination of advanced composites has multiple advantages, including extreme durability. “It’s meant to last a long time for rigorous use by first responders in very harsh conditions,” says Mulligan. The materials also make the drone extremely lightweight – between 24 and 36 pounds, depending on add-ons that include searchlights, loudspeakers, two-way radios and sonar systems. Weighing less than 50 pounds when packed in its golf bag-sized case, EMILY can also be checked as airline baggage. This makes it possible for a Hydronalix team to rush the aquatic drone to global emergencies. Most recently, the company sent a sonar-enabled aquatic drone to the Abaco Islands in the Bahamas to map the debris-strewn harbor after Hurricane Dorian so first aid ships could safely enter. EMILY mapped the harbor in a few hours, allowing a medical ship to enter the harbor within hours instead of several days. In another deployment, two aquatic drones rescued 360 Syrian refugees off the coast of Greece in a single week. With hundreds of thousands of drownings annually, Mulligan would like to see his company’s aquatic drones available on every pier, beach and ship just as manual life rings currently are. Hydronalix is now partnering with Robin Murphy, a professor in the Department of Computer Science & Engineering at Texas A&M University, to develop artificial intelligence that will give EMILY the ability to find those in distress without remote control, which will free up first responders for triage or other rescue tasks. For now, Mulligan is proud of EMILY’s success and its role as an ongoing tribute to its namesake, his daughter’s 13-year-old friend who was killed in an accident while the company was developing the technology. “We had this invention, and everyone was so distraught that we decided to name it after her,” says Mulligan. “She always wanted to help people, and that is the mission of this boat drone – to help people in need.”
SUBSCRIBE TO CM MAGAZINE
Composites Manufacturing Magazine is the official publication of the American Composites Manufacturers Association. Subscribe to get a free annual subscription to Composites Manufacturing Magazine and receive composites industry insights you can’t get anywhere else.