
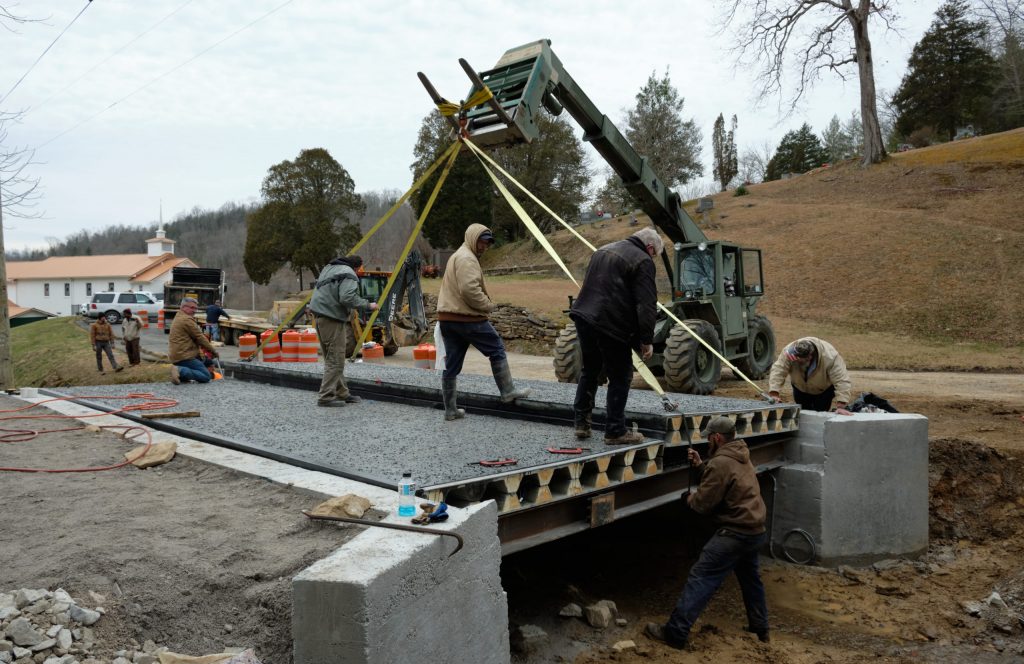
Bridge to Opportunities
You wouldn’t expect to find a bridge with state-of-the-art GFRP decking on a two-lane, rural road. But there’s one on Elizabeth Church Road in Morgan County, Tenn. Constructed through the efforts of a public-private partnership, the structure is intended to demonstrate the benefits of composite materials for bridge.
There’s a real need for this solution. The American Society of Civil Engineers estimates that 7.5% of the 617,000-plus bridges in the U.S. are structurally deficient and need repair. FRP composites offer a proven, low-cost, low-maintenance option.
Composites have been used for bridge deck projects for more than 20 years and have exceeded all of the performance and safety standards set by the American Association of State Highway and Transportation Officials (AASHTO), according to John Unser, vice president of program and project management at Composite Applications Group (CAG) and a consultant technology impact manager with IACMI – The Composites Institute®. The problem is that many highway directors and managers, especially those from smaller jurisdictions, still aren’t familiar with the technology.
The public and private entities that built the Morgan County bridge want to change that. Composite Applications Group, headquartered in Tennessee, and Structural Composites Inc., based in Florida, had already been exploring possible infrastructure opportunities with IACMI when the coronavirus pandemic hit. When normal business slowed and funding through the Paycheck Protection Program became available, the time seemed right to pursue a demonstration project. Because of its experience working with industry and government, IACMI took the lead.
Jeff McCay, CEO of CAG, discussed the composite bridge technology with Brian McKinney, president of McKinney Excavating in Tennessee. McKinney introduced McCay to Joe Miller, Morgan County’s highway superintendent, who was very interested in testing a composite bridge deck on one of the county’s distressed bridges. “One of the things that we think is pretty critical, especially in rural areas, is finding a champion,” McCay notes.
The group chose a bridge that is 25 feet wide and just 16 feet long. That short length was desirable since the Tennessee Department of Transportation does not have to sign off on bridges less than 20 feet long. (Concerns about risk mitigation may hamper state DOTs from approving new technologies.)
The bridge partnership then expanded to include researchers from the University of Tennessee’s Fibers and Composites Manufacturing Facility. They put together a system of fiber optic sensors, which was embedded in the composite decking during manufacturing, plus a module that enables the university researchers to monitor the structure over time. The sensors, developed by Luna Innovations Inc., will measure strain from mechanical loading and thermal/hygroscopic (humidity) loading from thousands of points.
“The lack of solid performance data has been one of the major roadblocks to widespread use of composite bridges,” says Dayakar Penumadu, the Fred N. Peebles Professor in the University of Tennessee Tickle College of Engineering and characterization fellow in the materials and processing group for IACMI. UT researchers and students will continue to monitor the bridge’s performance remotely through cloud computing. (The public can view monitoring data at compositebridge.org.)
“Although it’s a small span, it’s designed as a highway bridge deck, so all of the sensing data that we will be gathering is similar to what we would be seeing on a highway bridge. It’s a very low-risk way to gather real-time data that will give DOTs some confidence in the technology,” McCay says.
The team plans to develop a comprehensive case study comparing the total costs of a typical concrete bridge and one using an FRP bridge deck. “We will share the case study framework and results with federal, state and local officials, transportation departments and the civil engineering community so FRP composites will be more of a ‘known’ to them,” says Unser.
McKinney Excavating demolished the existing bridge and built the concrete foundation for the FRP composite decking. Other companies that contributed to the project included Compsys Inc. (PRISMA® composite preforms), Interplastic Corporation (resins), West System (epoxy resin), Superior Fiberglass and METYZ (fiber reinforcements) and AcraLock (adhesives).
All of the partners agreed to contribute their labor and materials. This was welcome news for Morgan County, which, like many rural communities, has a very limited budget for infrastructure repairs. Since the bridge has a 100-year life span, the county will also save money long term.
There was a benefit for Morgan County motorists as well. Since the bridge decking was manufactured in the factory rather than in the field, they didn’t have to deal with long, inconvenient road closures.
Structural Composites designed the bridge and built the decking in two modules, both measuring 8 x 25 feet. Each module consisted of two single-skin PRISMA preform sections, which were joined together in the factory at the raised frame caps.
“The two sections can be produced with a range of production methods, from low-volume open molding to closed molding to continuous molding,” says Scott Lewit, president and co-founder of Structural Composites. “They can be made to work with open molding/wet lay-up or adapted to infusion or to vacuum assisted resin transfer molding. This allows the technology to scale based on the manufacturing base and market demand.”
One technological breakthrough on the Morgan County bridge was the method of applying the asphalt wearing surface to the composite decking. This typically happens on-site after the bridge is installed. “We felt it was very important to get that out of the field and into an environment where everything was controlled,” says Lewit. “Our system comes with a technology – CoCure® combined with aggregate – that makes a super tough wear surface. The urethane component gives us a really strong adhesion to the deck.”
The completed bridge sections were placed on a flat-bed semi-trailer and transported to Morgan County. Because the sections were so lightweight, crews were able to install them in one day using a forklift. There was no need to rent a crane, which further reduced installation time and costs.
The bridge opened to traffic in the spring of 2021. McCay says that Miller is sold on the benefits of composite decking and hopes to use it again on other bridges that need repair. The Tennessee Department of Transportation (TDOT) has also expressed interest in the technology. “The use of fiber-reinforced polymer bridge deck units … has the potential to greatly enhance the performance, durability and service life of our low-volume rural bridge network across the state,” said Ted Kniazewycz, TDOT structures division director, in a statement.
The project partners are confident that the Morgan County bridge will serve as a model for other jurisdictions looking for cost-effective, long-term solutions for fixing their bridge infrastructure. While they hope the performance data they collect will convince state DOTs to try out the composite decking on larger bridges, they realize they have uncovered an urgent need in rural communities and found a solution that will work well for them. Lewit says he would like to see democratized or distributed manufacturing of the technology. That approach would allow local composite fabricators to build the decking components for bridges in their areas, bringing more jobs into those communities.
In the meantime, the bridge in Morgan County has already yielded many benefits. “It was a win/win/win project,” says McCay. “It was an opportunity to get a technology that could be a game-changer out in the marketplace, to do it in a community that has a need that gets fulfilled and to collaborate with other companies in the industry.”
SUBSCRIBE TO CM MAGAZINE
Composites Manufacturing Magazine is the official publication of the American Composites Manufacturers Association. Subscribe to get a free annual subscription to Composites Manufacturing Magazine and receive composites industry insights you can’t get anywhere else.