
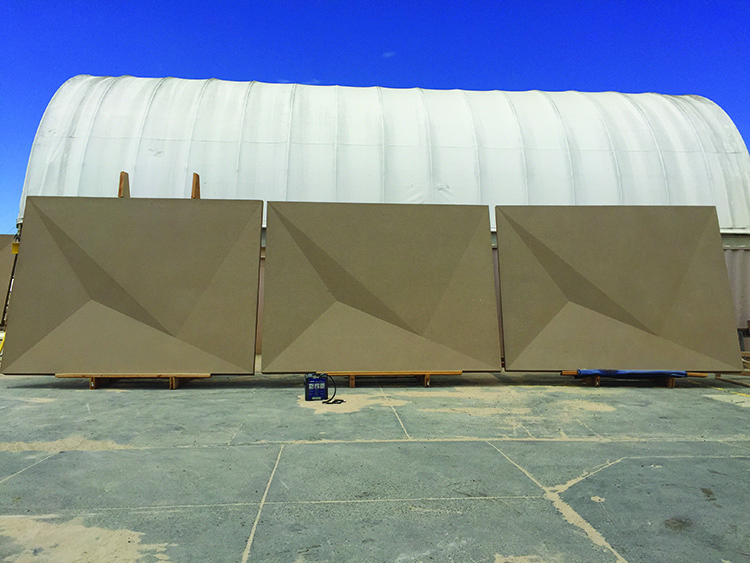
Color Matching and Control for the Fabricator
In the composites industry, many products require some sort of color specification, written or implied. It is important for fabricators to understand the basic elements of color and color control in order to keep clients satisfied.
For shops that mass-produce molded gelcoat finishes, the gelcoat supplier can do color matching. Fabricators may also consult with pigment manufacturers for help with matching in standard gelcoat bases. However, when compounding custom gelcoats or producing short-run products, in-house color matching can be more convenient. In both scenarios, it is important to monitor color of the final product to ensure the product meets customer demands. This column discusses how to match colors in house, specify a color tolerance, and monitor and control color throughout a project’s manufacturing period.
In-House Color Matching
Matching a client sample in house may seem daunting, but it can be done easily with a basic knowledge of color theory and a little practice. (While color theory is beyond the scope of this column, it can be learned from numerous online or print resources.) Gelcoat suppliers have color software that can calculate a pigment formula based on a measured color. Fabricators typically don’t have access to this software, and have to match by trial and error. A visual match can usually be attained within two to three rounds of color chip samples.
A good matching technique is to start with pigment pastes, which allow you to spend as much time as needed changing and shifting the color. Arriving at the correct pigment color is much like mixing primary colors of paint, except that it is critical to take careful weight records and notes after each addition or subtraction from the mixture. Samples of the pigment paste mixture can be taken to make samples at any time during the process to get a broader range of color options.
Once the pigment paste is close to the desired color, it is then added to the gelcoat base and cured to create a sample. Pigment loading amounts can vary based on color and pigment type, and the gelcoat supplier should be consulted for the proper loading amount.
Color shifts due to gelcoat base and processing are important to consider. Figure 1 shows the color shifts associated with a custom gelcoat mixture. The pigment mixture is cooler in hue and more saturated than the swatch to be matched. Once added to the gelcoat base, the color becomes warmer and slightly duller. Final processing for this color was a sandblast finish, which lightens the value and de-saturates the wet color. The final sample is close to the swatch but still a little too warm, requiring another round of matching.
When evaluating a round of color matching, it is important to consider metamerism, a phenomenon in which certain colors can match under one light source but not under another. To avoid issues with metamerism, it is important to evaluate matches under a controlled light source that mimics the lighting the final product will be evaluated under. A color meter can confirm a color match, but never underestimate the human eye, which can also discern very minor color shifts.
Specifying a Tolerance
Color tolerance is important to specify for any project and needs to be understood by suppliers, fabricators and clients. Many fabricators use a reference color placard and a trained quality control operator to check color. To ensure that color references remain true to color, they should be stored properly to avoid sun exposure and replaced at the supplier’s recommendations.
However, simply using a reference color placard may not suffice for color critical operations, such as architectural applications and mass-produced parts mated during assembly. For color critical applications, a color meter should be used to measure color and confirm it is within tolerance.
At Kreysler & Associates, we create visual tolerance boundary samples to illustrate the maximum allowable color shifts in each direction to the customer. The samples can be measured to create a tolerance. Often times, only a lighter and darker boundary sample are made, since that is the typical color variation for us. If other shifts are expected, samples can be made that illustrate more red, green, blue or yellow shifts. Customers can then use the samples on site to confirm product conformance. Fabricators without a color meter can use the samples as an internal quality control check.
In the coatings industry, Delta E units are used to express the measure of change in visual perception of two colors. A typical tolerance that gelcoat suppliers will meet is 0.5 Delta E. Beware that color can be shifted another 0.5 Delta E just from processing variation. For most applications, a 1.5 Delta E tolerance on color critical projects is acceptable to the client, but this can be hard to meet when using multiple batches of gelcoat. When mixing gelcoat in house, color can be corrected before use, but there will still be variation from processing. Although it’s not always possible, using the same gelcoat batch for all products is a great way to minimize color variation.
Monitoring and Color Control
Once a color has been chosen and a tolerance set, it is important to monitor the color and ensure that parts are within tolerance. Most fabricators let gelcoat companies handle color control, but monitoring incoming materials and final parts is just as important. At Kreysler & Associates, the most commonly seen issues with color are due to processing and incoming material. Controlling temperature, initiator percent, atomizing air pressure and release agent will help minimize color variation.
To ensure incoming material is not an issue, a color placard should be made with the same processing steps as the final parts for each gelcoat batch. The placard can then be used to verify that the incoming material will match. With a color meter, this match can be verified numerically and plotted on a control chart as a pre-emptive quality control step.
In summary, handling color in house offers benefits beyond the ability to control and quickly custom match. When tolerances are discussed and set up between the supplier, fabricator and customer, costly mistakes can be avoided. Once understood thoroughly, color can become a tool rather than a burden, allowing shops small and large to make unique products.
SUBSCRIBE TO CM MAGAZINE
Composites Manufacturing Magazine is the official publication of the American Composites Manufacturers Association. Subscribe to get a free annual subscription to Composites Manufacturing Magazine and receive composites industry insights you can’t get anywhere else.