
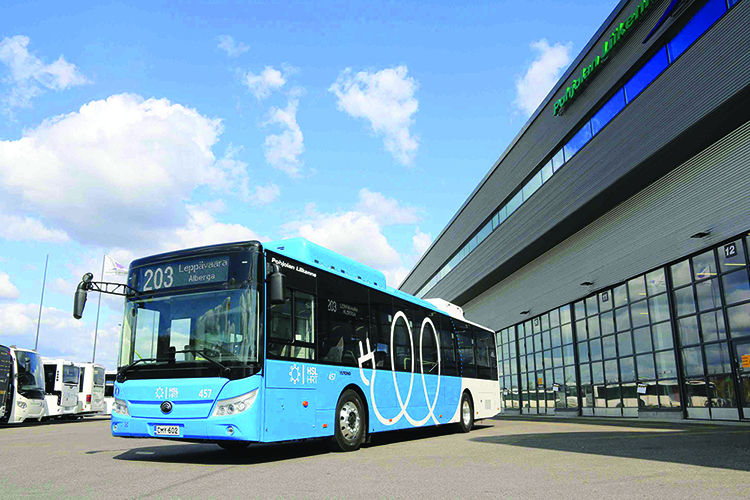
Composites Power Efficiency in Electric Buses
In November 2018, the Helsinki Regional Transport Authority in Finland (HSL) set an ambitious goal. By 2025, 30% of the buses on its service routes would be zero-emission, fully electric buses. Just nine months later, in August 2019, Chinese bus and coach manufacturer Yutong delivered 33 electric buses to the Finnish bus and road operator Pohjolan Liikenne.
This was the largest number of buses that Finland had ever purchased from an overseas supplier and the first time that Yutong had sold its electric buses in the Finnish market. While the buses were manufactured in China, there is a Finnish connection. The composite profiles for the vehicles were supplied by Exel Composites, headquartered in Vantaa, Finland, less than a half-hour drive from Helsinki. The panels were manufactured in Exel’s plant in China and delivered to Yutong, where they were attached to a fabricated steel frame during the bus manufacturing process.
Exel Composites has been involved with Yutong on this project for just over a year, but the company has had three decades of experience in manufacturing composite parts for buses, coaches and rolling stock, according to Jari Sopanen, Exel’s segment owner – transportation, vehicle solutions. “These panels were based on that legacy, and we worked closely with the customer to develop the properties that they wanted for them,” he says.
Exel designs and manufacturers some of the largest and most complex carbon fiber and fiberglass composite profiles on the market, according to Sopanen. While the Yutong GFRP bus profiles were fairly typical, they were at the larger end of the range, measuring 35.4 inches wide by 98.4 feet long.
The thermoset profiles were made with glass mats and polyester resins in a pultrusion manufacturing process. “We run sections, and then cut them to length at the end of the line. We then do the machining for the openings for wheels and other equipment,” Sopanen says. The art of the manufacturing process is in making the shape consistently and in achieving the high-quality surface that Yutong required.
By incorporating composite materials in their electric buses, Yutong realized several benefits, including lightweighting, better thermal management and corrosion resistance.
Glass fiber is one-third lighter than aluminum and one-quarter the weight of steel. In addition, composite materials have natural insulating characteristics that make it easier and more efficient to keep passengers cool in the summer and warm in the winter. Composite materials can further reduce the part count and the weight of the bus structure by incorporating many different features into one profile.
All of these lightweighting characteristics help the manufacturer improve the energy efficiency of the electric buses and extend the range they can travel between charging. Although electric buses are more costly to purchase than diesel-powered vehicles, the cost is offset over the years because of their lower energy costs.
Passengers on these electric buses are more comfortable, too, because parts made with composite materials produce less noise and vibration than similar metal parts. In addition, buses made with composite skirts and panels spend more time on the road because they don’t require treatment for body corrosion like buses made from metal. That’s important in Helsinki, which uses salt on its snowy roads in the winter.
“One other driver for using composites is freedom of design. If you want to have specialized designs on the long panels on the side of the bus, that would be quite challenging to do in metal,” Sopanen adds.
Finland’s adoption of electric buses reflects the European Union’s commitment to reducing the urban pollution that’s caused by buses. In 2019, the European Parliament set minimum targets for urban areas making bus purchases. Depending on a country’s gross domestic product (GDP), 24% to 45% of its cities’ bus purchases must be “clean” by 2025, and 33% to 60% must be clean by 2030. The EU dictates that half of those buses must be electric powered and the other half can run on liquefied or natural gas.
Exel, which produces composite parts for many European bus manufacturers, has seen a lot of interest in electric buses. “All of the manufacturers are looking at EVs now, plus there are new players coming into the market to supply electric buses,” says Sopanen. For manufacturers in search of lightweighting options, the company can provide skirting, side panels, internal coves, air ducts, ceiling profiles, flooring, luggage rack parts and cant rails (the section of the bus above the windows, which is canted or angled to connect with the roof).
The introduction of the Yutong electric buses in Helsinki has gone well, and HSL plans to have 400 fully electric buses operating in and around the city by 2025. This should help Finland meet its nationwide target of reducing carbon dioxide emissions by five million kilograms (about 11 million pounds) a year.
SUBSCRIBE TO CM MAGAZINE
Composites Manufacturing Magazine is the official publication of the American Composites Manufacturers Association. Subscribe to get a free annual subscription to Composites Manufacturing Magazine and receive composites industry insights you can’t get anywhere else.