
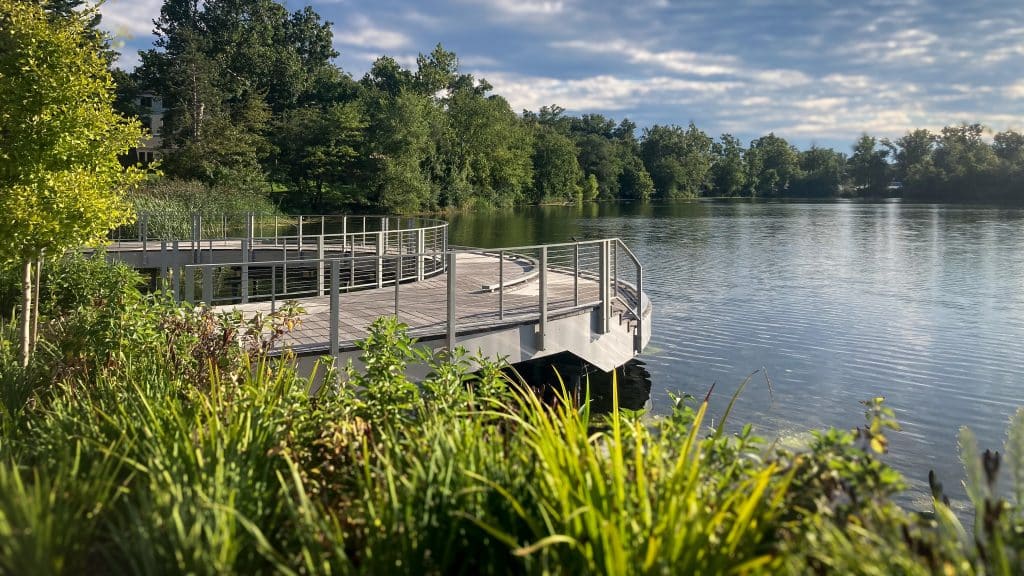
Creating a 100-Year Landmark at Notre Dame
The University of Notre Dame had two key maintenance requirements for the construction of its new campus landmark, Our Lady of the Lake World Peace Plaza. The structure had to last at least 100 years, and lifetime maintenance costs should be minimal. After the landscape architecture firm Hoerr Schaudt developed the design, the university tapped Frost Engineering & Consulting for the structural engineering work.
“We have worked with the university in the past on several other projects and have developed a good relationship with them,” says David Pirchio, project engineer at Frost. “So, when they came to us looking for some insights regarding the design of the platform and with those specifications, we said we were aware of just one material that could achieve that – FRP.”
Frost has been using fiber-reinforced polymer composites in projects for more than a decade. “We believe that these materials are going to attract more and more attention in the future,” says Pirchio, who researched composite materials while earning his doctorate from Notre Dame. The World Peace Plaza provided an excellent opportunity to display FRP’s advantages as a building material.
The plaza, located along St. Mary’s Lake, is a legacy gift from the family of Wiilliam Pulte, the founder of the Pulte Group, one of the country’s largest homebuilders. Its central point is a 2-foot-high, 18-foot-diameter black granite fountain inscribed with a prayer for world peace in six languages – English, Spanish, Hindi, Arabic, Mandarin Chinese and French. (According to the University of Notre Dame, 97% of the world’s population can read at least one of those languages.) The fountain is surrounded by circular rows of stone, and the structure rests on a 69-foot-diameter concrete mat foundation.
The plaza’s lakeside location and the university’s longevity requirements ruled out using traditional steel rebar for reinforcement of the concrete mat; steel would corrode, and the concrete would break down. Working in collaboration with Hoerr Schaudt and the university, Frost specified pultruded FRP rebar to reinforce the concrete mat as well as the curved, cast-concrete benches on the plaza’s perimeter.
“FRP addresses a critical need for durable, low-maintenance public spaces, especially in challenging environments like waterfronts where traditional materials, such as concrete and steel, often degrade quickly and require frequent upkeep,” says Pirchio. He notes that steel and concrete are especially vulnerable to corrosion in cold weather areas like the Notre Dame campus, where salt is frequently used to keep pathways clear in snowy weather.
The boardwalk’s structural support beams, sub-decking and railings are also all pultruded FRP. In addition to their inherent resistance to corrosion, another advantage of using FRP for these elements was their light weight. The material was easier to handle than steel or wood and required less equipment to install.
To keep construction costs as low as possible, Frost specified the use of off-the-shelf pultruded FRP sections. “We try to avoid any special requirements because we want our clients to have the option of buying from multiple manufacturers so they can receive competitive bids,” says Pirchio. It did take some detailed engineering to angle the straight FRP sections to form the required semi-circular shape of the boardwalk.
While strength is rarely an issue when replacing steel structural elements with FRP ones, the composite components had to be carefully chosen to avoid any problems with deflection. “We don’t want the boardwalk to bend or vibrate too much when people are walking or running on it,” Pirchio adds.
The other challenge with using FRP is forming good connections. FRP connections can be more complex to design and detail than steel connections because of the different material properties. “So, you have to build up your experience, go back to the basics and trust your calculations,” Pirchio says. The team selected stainless steel bolts that should hold the components firmly in place for the required 100 years.
Frost partnered with fabricators of pultruded FRP components to ensure the various design elements met the project’s durability and sustainability requirements.
“Working closely with FRP fabricators ensured that the plaza's structural components could withstand environmental challenges while maintaining high standards of quality and performance,” says Pirchio. Frost also specified that the material must contain UV inhibitors.
With the FRP structural elements, the University of Notre Dame can expect to save up to 75% on maintenance costs when compared to traditional steel and reinforced concrete structures, according to Frost. Pirchio notes that these advantages align with modern sustainable construction practices, which take total life cycle costs into consideration when it comes to design and materials selection.
The construction of the World Peace Plaza has set a precedent for integrating innovative design and materials into future infrastructure and architecture projects and encouraging collaboration among architects, engineers and composites manufacturers on such projects.
“Hoerr Schaudt’s design input enhanced the plaza’s attractiveness and functionality, making it a more appealing landmark within the campus and broader community,” says Pirchio. “This aesthetic appeal contributes to the plaza’s role as a symbol of innovation and sustainability.”
SUBSCRIBE TO CM MAGAZINE
Composites Manufacturing Magazine is the official publication of the American Composites Manufacturers Association. Subscribe to get a free annual subscription to Composites Manufacturing Magazine and receive composites industry insights you can’t get anywhere else.