
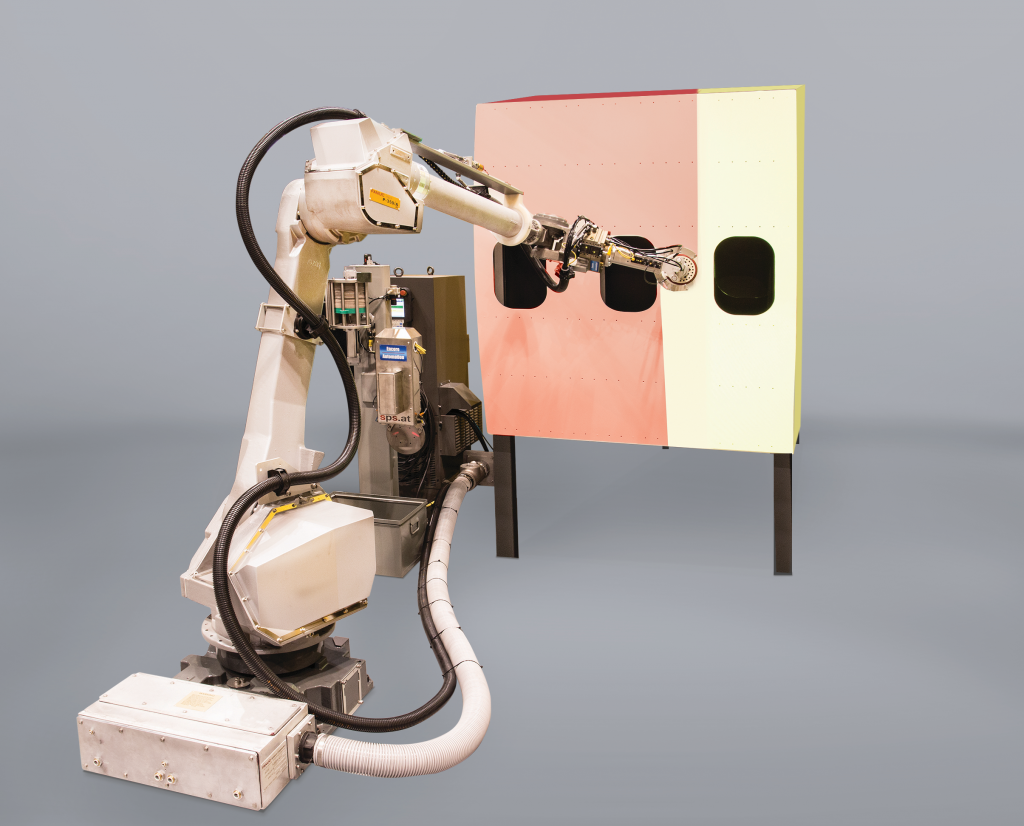
Finishing Touches
Structural engineers and process managers tend to focus on materials, infusion, bonding and assembly when they discuss the manufacture of giant wind turbine blades. “But the reality is that only represents about 55% to 60% of the total manpower hours that go into the blade,” says Steve Nolet, senior director of technology and innovation at TPI Composites Inc. “There are a tremendous number of operations that have to occur downstream of that infusion and assembly stream.”
TPI produces wind blades for numerous wind turbine manufacturers, and the processes vary slightly by blade design and customer preference. But manufacturing typically begins with lay-up and infusion of both the pressure side and the suction side of the mold halves. After that process is complete, the blade sections remain in the molds for assembly.
The next step is to bond shear webs onto a blade section, usually the pressure side. Epoxy bond paste is dispensed onto the surface of the spar cap in the mold, prior to the final location and placement of the shear web. The placement process is machine-assisted; bridge cranes equipped with large gantries pick up the shear webs, and the operator moves them into the general position along the blade. Using registration points to determine the exact location, the gantry places each web and holds it in place until the epoxy bond cures.
“The placement of the shear web is very accurate; we have about a 5-millimeter tolerance allowed on an 80-meter-long layout,” Nolet explains.
Composite technicians then apply epoxy bond paste to all the blade and shear web surfaces to be bonded and close the mold to join the pressure and suction sides of the turbine blade together.
Automating Finishing Processes
Manufacturers of aerospace and automotive composite components have automated many of their lay-up and assembly processes.
“Aerospace assembly is a combination of manual/hand and automation,” says Rick Schultz, aerospace program manager at FANUC, an automation solutions provider. “The aerospace primes are constantly evaluating ways to improve automation. The main benefits of increasing automation are higher levels of accuracy and less need for rework. With the size and cost of most aerospace composite parts, the improved consistency of application that automation enables helps minimize the costly rework and scrapped parts.”
While the wind blade industry would benefit from that same kind of consistency, robotic systems aren’t fast enough for that volume of lay-up work.
“With the kind of automation that you see in the aerospace industry, the machines are depositing materials at a rate of something on the order of 50 to 100 kilograms per hour, which is a fantastic rate,” explains Nolet. “But a wind turbine blade over 18 metric tons; imagine how long it would take for a machine to lay that up at 100 kilograms per hour. We want a 24-hour cycle time.” It takes a crew of at least eight people to do all the lay-up and preparation work in this time frame.
In addition, the prepregs required for automated systems cost much more than the dry reinforcements and infused resins that TPI uses now.
For wind blade production, finishing operations are a better fit for automation. TPI’s finishing work begins with the demolding of the complete blade, the removal and fairing of any flash on the leading and trailing edges of the blade, and the application of wet laminates to those edges to cover the seam. “Technically, it’s an effective method of shear transfer to tie the pressure side to the suction side,” says Nolet.
After the laminates have cured, the blade surfaces require sanding and fairing. That can be done manually or, for the last decade, with multiaxial robots equipped with vision systems and compliant sanders. The automated systems use tactile feedback to determine how much pressure to apply on each area of the blade. “When you touch a surface, it creates a force of resistance. A tactile and compliant robot will sense that resistance and back off to maintain a uniform pressure over the blade,” Nolet adds.
The next finishing step is the machining of the blade’s root – the portion of the blade that fits into the turbine’s hub. “The blade is presented to a built-for-purpose machine that will mill the end of the blade to a very flat face – within half a millimeter of plane,” says Nolet.
The process varies according to the turbine manufacturer and the method of blade attachment to the turbine hub. In some cases, the machine drills up to 84 separate holes in the milled root axially to accommodate the installation of a threaded stud and radially to accommodate a nut that locks in the blade’s connection to the hub. These processes are mostly automated, although there is an operator standing by to make sure everything runs smoothly.
Some manufacturers are now taking an alternative approach, inserting bonded threaded female inserts that accept the threaded studs in the blade root as part of the molding process. During finishing, the machining equipment mills the root with the embedded studs to the desired flat surface.
The newer process is a trade-off, says Nolet. It takes less time at the finishing stage and allows for the insertion of more studs than the drilling process. That adds strength to the blade/hub connection. But the inserts are more expensive, they require more labor to place them into the mold before infusion and they add time to the molding cycle.
Finding a Good Balance
During the blade lay-up stage, TPI usually applies a gel coat to the surface of the mold to reduce pin-holing on the blade surface and to prevent the cured material from sticking in and damaging the mold. But the gel coat leaves a glossy finish on the blades.
“It’s a terrible surface for adhering paint to, so if we’re going to get our coatings to adhere, we have to scuff-sand the surface to make it ready for painting,” Nolet says. “That’s another process that lends itself to different forms of automation, either human-assisted automation using different tools that can quickly scuff the surface or robots that can perform a compliant sanding operation.”
The blades then go into a painting booth where robot sprayers, or people using rollers or high-velocity, low pressure sprayers, apply a primer and a finishing coat. The improvement of all-in-one coating systems, where the primer and the topcoat can be applied in a single application, could save time in this area of finishing, Nolet says.
It’s around this time that technicians tie out the lighting protection system. Metallic receptors and cables that act as lightning rods are molded into the blade and must be connected to one of the root studs to be effectively grounded.
The last step, the balancing of the blades, involves adjusting the mass and center of gravity on the three blades that will be installed on the same turbine to ensure that they are consistent. If the blades aren’t balanced, the turbine won’t operate properly.
Each blade has balance boxes installed during the molding process. There are usually two or three distributed at the blade root and the tip. After measuring the mass of the blade (using two load cells) and determining its center of gravity, technicians add sand with epoxy to the balance boxes to reach the desired mass moment of inertia. The amount of this mixture and where it is placed are carefully calculated.
“We’re balancing the blades very closely,” says Nolet. “If the center of gravity is off by even 100 millimeters that will make a difference in the swing weight and the balance.”
Once the blade is balanced, inspectors give it a quality check – the last of many that have been performed throughout the entire manufacturing process. The blade then receives a decal or a stencil with the manufacturer’s name and a serial number.
The Future of Finishing
At most of TPI’s manufacturing factories, half of the space is dedicated to molding operations and the other half to finishing. When operating 24 hours a day, five days a week, a four mold-set factory will produce 20 blades per week – or about 1,000 blades per year, based on the desired 24-hour molding cycle.
The capacity of the plant is dictated by the speed of the lay-up, assembly and demolding processes, which take about 24 hours in elapsed time per mold set. The finishing stages take about twice as long in elapsed time, and there may be 10 to 15 blades in the finishing queue at any time, says Nolet.
“From the start of the molding of the blade to the time it rolls out as delivered is about 72 hours,” he says. Automation could speed up that process. The development of 3D models will help manufacturers improve the accuracy of blade assembly, and the adoption of robotic systems for finishing will become more widespread as those systems become more capable.
But automation brings its own challenges. Product cycles today are short, and blade shapes frequently change. If a wind turbine manufacturer only wants 500 blades of a particular design, it’s difficult for blade producers to justify the cost and time it would take to implement an automated setup. Robotic manufacturers are looking at ways to make their systems more adaptable to different designs, Nolet says.
Another challenge is planning for the space required by the automation technology. That must be done early in the plant design to incorporate it into the process flow. If a new automated system calls for a bridge crane, it’s usually not possible to retrofit an existing plant to accommodate it.
The changeover to increased automation in finishing will be gradual, Nolet adds. “You won’t see the difference in the next six months, but you will see that difference over the course of years, another couple of generations of product cycles. I think there'll be more effective automation being employed because of the response of system integrators to improve the adaptability of robotic systems.”
Mary Lou Jay is a freelance writer based in Timonium, Md. Email comments to mljay@comcast.net.
SUBSCRIBE TO CM MAGAZINE
Composites Manufacturing Magazine is the official publication of the American Composites Manufacturers Association. Subscribe to get a free annual subscription to Composites Manufacturing Magazine and receive composites industry insights you can’t get anywhere else.