
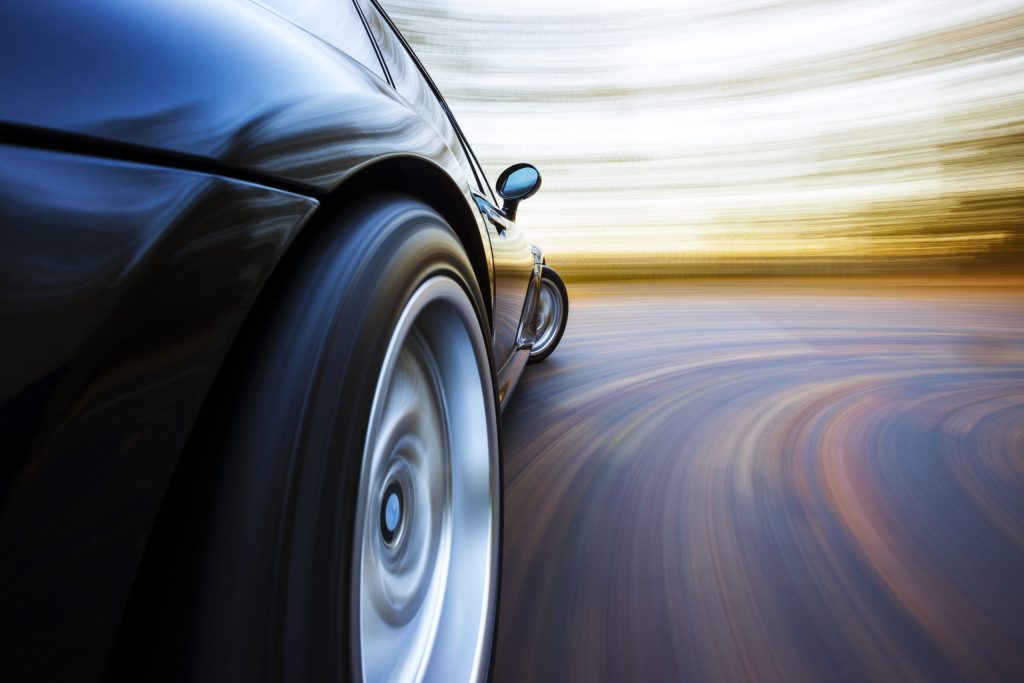
Positioning Composites in Automotive Production
As the automotive product landscape continues to change in multiple directions, business cases and market entry points for materials also change. Depending on the automaker, engineering team and even the target market consumer base, environmental implications of a product’s life cycle are a metric with a long history of frameworks and reporting. Niche brands and vehicle nameplates have grown anew through a rigorous focus upon the business details, which impact recycling, landfill waste, energy efficiency and even raw material sourcing. While the current megatrend is “it’s cool to be green,” the details of business conduct at an engineering level are changing from single metrics of performance to holistic process evaluation. Finding the right customer for your material in this market is as much a matchmaker effort of relationships as it is a collaboration of establishing the right overall impact. As a society and as an industry, we are all being challenged to cross train and evaluate decisions beyond math and science, venturing into a subjective set of critical thinking. Lightweighting of automotive components is a marathon effort in which the composites industry is no stranger to the diverse applications and operating conditions of components. Interior components may represent the largest collection of composites for current automotive products. However, as an industry, we must remember and look forward simultaneously – remember that many interior components were once made of different materials, while looking forward to the next applications emerging in the industry. Emerging Applications As energy storage devices are changing in market diversity and materials, the composites industry already shows advancements and benefits. There is opportunity for growth in the use of polymer-based materials for both internal combustion and battery electric vehicles, as is evidenced by recent applications for FRP fuel tanks and lines and battery pack lids made from sheet molding composite (SMC). But with that opportunity comes challenges, too. In some cases, composite construction provides an opportunity for customer excitement. In other cases, the performance of composites enables entire business cases, such as compressed natural gas (CNG) and hydrogen storage tanks. While some regions have embraced CNG vehicles because the carbon offset and cost performance make them economically viable, the technology does not gain a majority share in our automotive sector outlook. In India and Oklahoma, for instance, CNG pumping stations are convenient enough to normalize the fuel decision, but the market has largely stagnated for this fuel. The simplest rationale comes from the costs to produce the fuel system components. Tanks expire before the useful life cycle of the vehicle, especially when in a light or medium duty commercial application, which leads to vehicles being scrapped instead of maintained. However, a high-level viewpoint of economics provides a blunt rationale for dampening of wound tanks: If a technology and manufacturing method does not have a home within higher price-point markets, such as aerospace or racing cars, it will not reach mass adoption without significant improvements involving disruptive technologies. Manufacturing development is expensive and largely subsidized by such high-end markets. This is largely a statement of the nature of automotive as a nexus point of technologies where industries overlap, market timing is critical and passenger cars are both the progenitors and adopters of technology trends. Touchscreen displays and Phillips-head screws are ubiquitous in devices sold today, and both had roots in the automotive industry long before other industries adopted these solutions. Contrary to those two examples, technology such as carbon fiber and turbochargers largely evolved outside of automotive before adoption within. Each one of these product examples has a particular pathway to economic growth and a particular foothold within the marketplace. Aligning Materials to Needs As we look to composites usage in automotive body structures, the similarities to other technologies reveal a landscape whereby the competition of materials can determine where best to employ a solution. Disruption occurs when you break the boundaries of these market competition conditions. Cost advantages, material performance or even formability can all take a product to the next level of opportunity, but alignment of materials to functional engineering needs is key. Within bodies, rear closures are quickly moving toward GFRP composites for not only weight savings, but also the secondary benefits at the assembly plant level. (See Figure 2.) The aforementioned change in mentality toward a more complete evaluation means that solutions trading one metric for another without a secondary benefit are less likely to pass rigorous examination of any large engineering firm with an established background. Otherwise, as one engineering mentor stated at General Motors, “Good engineers trade performance with an ‘or’ statement. Great engineers look for an opportunity to create ‘and’ statements in designs.” Examples of “and” statements include providing value and customer benefits, losing weight and costing less overall, and reducing ergonomic strain of plant workers and improving component packaging. Growth areas, such as rear closures and battery enclosures, appear as easy opportunities for near-term manufacturing, but the power of composites goes well beyond this short-term sprint. Innovations in reinforcement fiber types, cross-linking resins, pultrusion and higher levels of electrical insulation are great examples of mid-term rule-breaking technologies that stand to challenge the status quo of the mechanical and electrical devices currently being produced for high-volume passenger vehicles. The history of the ceramics industry during the manufacturing adoption of spark plugs is one of the historical parallels that might be used to describe the opportunities in front of the composites industry today. Composites have the power to use waste carbon fiber from aerospace manufacturing and to adopt higher temperature resistances than most aluminum alloys. Depending on resin choice and fiber reinforcement, composites may be the only material that can outperform the net zero-emissions goals by sequestering carbon emissions to become the only certifiably carbon negative substrate for component construction. All of this is stated without imparting the enormous passenger safety responsibility of OEMs chasing higher electrical motor voltages. The technical capability ingredients of material performance are present in many corners of the composites market, but the true challenge lies ahead: Build the components in repeatable processes at high volume in simple ways that dovetail with engineering, maintenance and assembly ideologies. Edwin Pope is principal research analyst in the Supply Chain & Technology Group at S&P Global Mobility. Email comments to edwin.pope@spglobal.com. Figure 1: Composites Market Competition Index
Credit: S&P Global Mobility Figure 2: North American Rear Closure Market Share
Credit: S&P Global Mobility
SUBSCRIBE TO CM MAGAZINE
Composites Manufacturing Magazine is the official publication of the American Composites Manufacturers Association. Subscribe to get a free annual subscription to Composites Manufacturing Magazine and receive composites industry insights you can’t get anywhere else.