
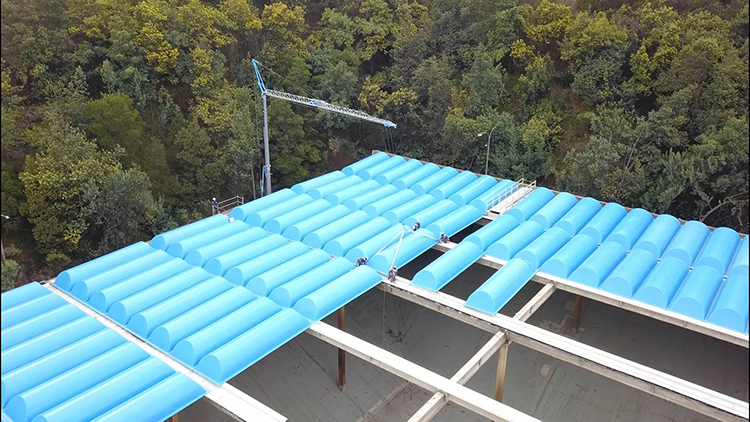
Protecting Potable Water in Colombia
Colombian composites firm Soling SAS recently manufactured 840 GFRP dome panels to cover the country’s largest potable water tank, providing a durable and aesthetically-pleasing solution that will protect the capital city’s drinking water supply from contamination for decades. In doing so, Soling also broke the country’s record for the largest part by volume produced using light resin transfer molding (LRTM).
The project began in 2019 when the Bogota Water Utility asked Soling to develop a new cover system for the 167,902-square-foot concrete tank. Built in 1971, the tank’s aging asbestos and concrete covers were increasingly difficult to repair and a risk to public health.
Soling’s engineering team chose to replace the flat cover panels with 25 x 8-foot GFRP semi-circular domes. The geometry ensured the best mechanical resistance, which was key to protecting the cover from children participating in a local pastime – throwing stones onto the tank from the surrounding hillsides.
Designing each 306-square-foot domed part to be light enough for the existing concrete support columns was tricky. “Weight was the biggest challenge to this project,” says Rodrigo Vergara, engineering coordinator at Soling. “We could not exceed the load capacity of the current structure.”
This meant that each cover component had to weigh less than 706 pounds. While Soling had extensive experience using open molding technologies to produce tanks and other water applications, the strict weight limit required a new approach – LRTM. “It was just not possible to do it any other way other than closed mold to limit the weight of the laminated covers. Open mold wasn’t an option,” says Andres Collazos, Latin America sales manager for Magnum Venus Products (MVP), Knoxville, Tenn., which provided equipment and technical assistance along with local distributor Minepro SAS, Medellín, Colombia.
In addition to helping lightweight the massive parts, LRTM also provided an aesthetically pleasing finish. “The client didn’t want a pipe-like GFRP. They wanted a shinier, beautiful cover and they wanted two colors – a blue exterior and a white interior,” Vergara says, “The only way to meet these specifications was light RTM.” He says LRTM also provided 100% uniform parts.
Speed was another challenge. The water utility wanted the cover installation completed in one year, which required fabrication of eight domed parts per day. Twenty composites technicians at Soling worked on a 24/7 fabrication schedule using two molds, injection equipment and a two-color spray paint machine to produce 840 domed parts in 18 months, finishing in November 2020. “We worked every day and night. We didn’t stop,” says Vergara.
The fabrication process began with a spray application of two isophthalic gel coats – white on the bottom mold and blue on the top counter mold. Technicians then climbed into the mold and laid up 2- to 4-layer combinations of chopped glass fiber mats and two multidirectional mats from Jushi. The mold was then vacuum sealed and injected with Andercol thermoset polyester resin. The project used two tons of resin per day. Total fabrication time per part was four hours, including a 40-minute injection cycle.
The only piece that did not inject correctly was the first test piece. After the resin was reformulated for lower viscosity and a longer gel time and the brackets holding the mold and counter mold together were adjusted to better hold the perimeter vacuum, all of the domed panels were fabricated without interruption – or waste. “That was a huge win because when you estimate that the 706-pound part includes 461 pounds of resin, mistakes are an expensive undertaking!” Collazos says.
As each batch of cover parts was completed, they were immediately shipped 30 at a time to the installation site and installed by crane. The water utility and Soling were very pleased with the results. “We were able to take advantage of all the attributes of this type of material,” says Soling SAS CEO Javier Moreno. “We reduced the weight of the covers and at the same time increased the mechanical performance, aesthetics, system safety and the quality of water stored in the tank. Having made the largest part manufactured in the region using the light RTM process opens up opportunities for similar applications.”
While Soling now has the equipment and expertise to tackle LRTM applications, the company is an outlier in the region. Collazos says that open mold fabrication remains dominant because of low labor costs and other factors, but that is beginning to change. “We have noticed an uptick in demand for closed mold solutions,” he says. “But this is a recent development. Two years ago, there really wasn’t much at all.”
Soling is currently considering its next LRTM applications, including underground electrical boxes. Meanwhile, Collazos sees enormous opportunities for LRTM in fabrication of large panels for municipal and interstate busses. “That is a huge business in Latin America,” he stresses. Whatever is next, Soling is ready.
SUBSCRIBE TO CM MAGAZINE
Composites Manufacturing Magazine is the official publication of the American Composites Manufacturers Association. Subscribe to get a free annual subscription to Composites Manufacturing Magazine and receive composites industry insights you can’t get anywhere else.