
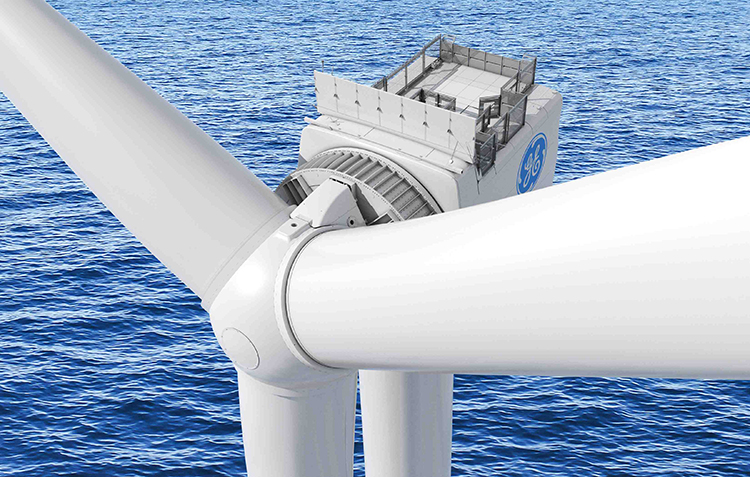
Embedding Sensors for Smarter Manufacturing
The wind energy industry is growing in the United States, and that means the country is going to need tens of thousands of new composite wind blades in the next decade. In 2019, it took more than 60,000 wind turbines to generate 109,919 megawatts (MWs) of electricity in the United States, Guam and Puerto Rico, according to the American Wind Energy Association (AWAE). Between projects already underway or currently in the final planning stages, AWAE projects another 44,000 MWs of wind power will be added over the next few years.
The hitch is that manufacturing a wind blade is currently a time-consuming and labor-intensive process. For example, GE Renewable Energy reports that it takes two days and 100 workers to produce a single 351-foot wind blade for LM Windpower’s factory in Spain. Although these are some of the longest blades manufactured today, the process is similar regardless of the blade’s length.
To improve and streamline the manufacturing process, a multidisciplinary team, led by GE Research, is currently investigating the feasibility of embedding sensors into GFRP wind blades during production. The sensors would measure temperature, resin flow and curing as the blade is being manufactured, with the goal of reducing cycle time, material usage and overall costs. The research is being funded by NextFlex, one of eight Manufacturing Innovation Institutes established by the U.S. Department of Defense as a public-private partnership. (IACMI – The Composites Institute is another.)
Through its consortium of 100 companies, academic institutions, non-profit organizations and government agencies, NextFlex works to foster the growth of flexible hybrid electronics (FHEs) in U.S. manufacturing. FHEs are formed by placing integrated circuits (ICs) and other electronic components onto flexible, stretchable and conformable substrates, such as film. This reduces the weight and size of these electronic circuits and opens up the possibility of incorporating them into products in many new forms. FHEs are currently being tested for medical wearables, asset and structural health monitoring systems, flexible array antennas and soft robotics.
“The advantage that you get with FHEs is that you can build electronics in form factors that you typically can’t [build] with conventional electronics,” says Scott Miller, director of technology at NextFlex. “You also have the potential to do some really important size, weight and power trade-offs that you couldn’t get without the lightweighting of the electronic systems.”
Building the Sensor
NextFlex consortium members selected the GE Research sensor project because of their widespread interest in using FHEs for asset monitoring. Nancy Stoffel, principle engineer of GE Research’s electronics and sensing group, is the team leader, and Shridhar Nath, GE’s platform leader for onshore wind, is the expert in wind blade technology. Binghamton University in New York is contributing knowledge and experience in electronics manufacturing, reliability and material systems, while Georgia Tech brings expertise in additive manufacturing of flexible radio frequency (RF) modules and passive wireless sensors. The project team will also create embedded sensors for carbon fiber composites, and helicopter manufacturer Sikorsky is participating to guide the specifications and needs for monitoring the structural health of aircraft components operating in the field.
The team’s early challenges included designing the sensors and finding a way to insert them into composite material without affecting its structural integrity. The sensors had to be wireless because running exterior wires could attract lightning strikes in the field, and since they were embedded, had to be passive and able to operate without battery power.
The team designed a passive, wireless sensor with a specific resonance frequency. When an electronic device called an interrogator sends out an energy wave, the sensor reflects it and the interrogator reads it. Changes in the resonance frequency or amplitude shifts in the reflected energy wave provide an indication of what’s going on inside the composite material.
“There are a couple of things that go into making the decision about what frequency bands to use,” says Stoffel. The team wanted the sensors to operate in ISM radio bands, which are reserved internationally for industrial, scientific and industrial purposes. To control costs, it decided to use the same interrogation devices used by automotive radar detectors that operate in the 25 GHz range. “This isn’t a large application where it makes sense for you to have a custom chip,” Stoffel explains.
“One of the challenges that we have is that we are burying [the sensor] inside the composite, which will modify it somewhat,” she continues. Embedding sensors into the composite also makes it more difficult for the interrogator to read. The team wanted the reading distance to be at least 6.5 feet. This would allow the interrogator to be suspended above the blade mold in the factory, so it could read data from the sensors without interfering with work on the production floor.
An additive printing process is used to manufacture the sensors. An aerosol jet printer sprays conductive metal inks onto a substrate such as a polyimide film. The printed circuits made through this process are fairly complex and include an array of small antennas (called the Van Atta array) to provide a good reading distance, according to Stoffel.
Minute changes in the spacing of the arrays will alter the response of the sensors, so they can be tuned for various properties. That made it possible to use the same sensors for both the GE production monitoring part of the project, including the extent of curing and the real-time temperature of the composite, as well as the longer-term, in-the-field strain monitoring that Sikorsky is testing.
Eventually, Sikorsky hopes to embed the sensors in a helicopter tail boom, which holds the tail rotor assembly, and use an interrogator to read the sensors on the aircraft in the field between flights. “Whether it’s a wind blade or the composite fuselage on an aircraft, the sensor is essentially giving you information about the life of that asset so you can manage it that much better,” says Nath.
A Scalable Process
The printed sensors measure only 2 x 3 inches and are thinner than a composite ply. Although the thickness of the sensor was important to minimize its impact on the composite structure, the goal wasn’t to get the smallest sensor possible, but to develop one that would fit easily into the shape of the wind blade. The team is also investigating how many sensors would be needed to get the data it wants and where those sensors should be placed.
The researchers will not build an entire wind blade to test the concept, but are trying to demonstrate that it is possible to add monitoring FHEs to a composite material in a scalable way, according to Miller. “One of the specifications was that the project team would have to produce a composite structure with embedded FHEs that was at least three square feet,” he says. While that’s not a large size in the composite world, it is large enough to show that the insertion of FHEs could be automated and would not require a precision, hand-assembly process.
“Wind blade manufacturing is a labor-intensive process, and things haven’t changed in the last 50 years,” says Nath. “There’s a big push to go from a conventional labor-intensive process to an automated process like what’s used for automotive production.” Another driver is that wind blades are getting longer and longer, which increases manufacturing cycle time. “You want to reduce cycle time and the labor footprint, and having sensors during manufacturing could help us do that, as well as monitor the health of the blades,” adds Nath.
For example, sensors can provide real-time information about how the resin is flowing, which will help automate the resin infusion and minimize the involvement of people on the factory floor. That information will help manufacturers optimize the use of materials by reducing weight, improving the quality of the composite and reducing cycle time, says Nath.
Extending the Application
The team has made good progress since beginning the project in January 2020. They have designed and manufactured the sensors, built some coupons with embedded sensors and proven that they are able to read them wirelessly. They are currently doing coupon level mechanical tests to make sure that the strength of the composite has not been impacted by the insertion of a sensor. (The team declined to share details on how it has achieved this.) Due to COVID-19-related delays, the project will probably extend a few months into 2021.
The preliminary results have been promising. Stoffel says that once the team has successfully completed the initial project, GE will be able to implement the sensor technology into its businesses. Sikorsky would like to build upon the initial project’s work by creating a customized, field-ready interrogator, using available parts and components, that could read all of the embedded sensors at once.
There’s a variety of applications where smart composites with embedded sensors could be used, ranging from rotating and structural components in aircraft to riser pipes in the oil and gas industry. The use of reliable embedded sensors will be critical for structural health monitoring and condition-based maintenance approaches, increasing long term performance, assuring that maintenance is done when needed and reducing cost and downtime. “That is the innovation part,” says Nath. “These are passive, wireless sensors that can be embedded and read remotely, and hopefully we can leverage that technology.”
SUBSCRIBE TO CM MAGAZINE
Composites Manufacturing Magazine is the official publication of the American Composites Manufacturers Association. Subscribe to get a free annual subscription to Composites Manufacturing Magazine and receive composites industry insights you can’t get anywhere else.